Singapore Sterntube Spill Reduced by Hydrex Mobdock
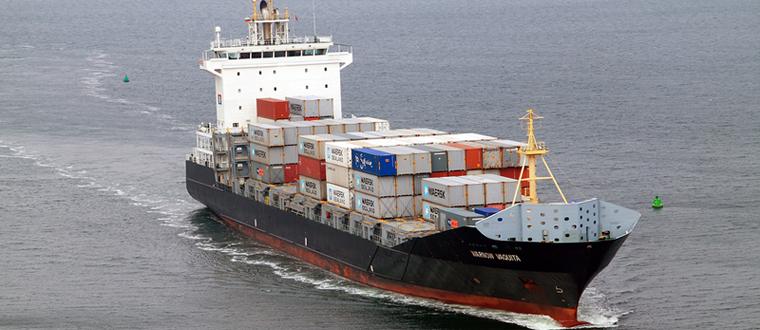
It is estimated that damaged ship sterntubes are leaking some 57 million tonnes of lubricating oil in to the oceans every year, but by replacing these seals when the damage is first discovered, Hydrex in-situ repairs not only help towards reducing the environmental impact but can also save shipowners time and money.
Using its flexible mobdock technology, damaged aft sterntube seals can be quickly replaced underwater during a vessels port-stay, negating the need for costly drydocking. Even complicated sterntube configurations and liners can be repaired this way.
“Environmental considerations are frequently demanding that damaged sterntube seals are repaired as they happen and in the shortest possible time frame,” said Hydrex Production Executive Dave Bleyenberg. “Every Hydrex office is equipped with the mobdock technology and sophisticated equipment that can be deployed at a moment’s notice to effect repairs in any location around the world.”
A recent sterntube seal replacement Hydrex engineers completed in Singapore underscores the commercial and environmental benefits of using the in-situ repair method.
When a 138m long LNG tanker began leaking oil from a damaged sterntube seal during the vessel’s port of call, an expedient repair was required to avert any delay to its schedule and prevent further pollution.
“Such incidents not only result in off-hire costs and charges, but also pollution related fines,” said Bleyenberg.
Hydrex’s local mobdock team was deployed while the company’s technical department in Antwerp, Belgium, put forward a detailed repair plan which, once approved, allowed the mobdock team to make all necessary vessel preparations. Within a matter of days diver/technicians were on-site carrying out the seal replacement work.
Working in concert with the original equipment manufacturer, the Hydrex team removed and replaced three damaged seals with new ones. The entire operation was carried out underwater, without the need to drydock the vessel and without disruption to the vessel’s schedule.
“From the start to finish, the project took just a few days, preventing any further oil leaks and keeping the vessel operational without incurring significant costs,” said Bleyenberg.