Ballast Water: A Decade Later, Alfa Laval PureBallast is Still at the Innovation Forefront
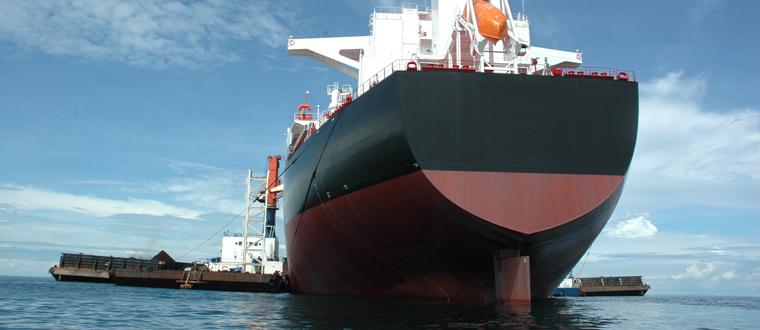
A decade has passed since Alfa Laval PureBallast first took to sea as a full-scale pilot, yet the ballast water treatment system continues to stand for innovation. With its unique combination of capabilities – including operation in fresh, brackish or marine water and in low-clarity water with just 42% UV transmittance – PureBallast is a system against which others are benchmarked.
When Alfa Laval launched PureBallast commercially in 2006, it was into a market full of uncertainty. Little was clear about the real-world challenges of meeting the IMO Ballast Water Management Convention, to say nothing of when it would take effect.
Today matters are different, with the IMO legislation nearing implementation and the USCG Ballast Water Discharge Standard already in effect. As more treatment systems are negotiated and installed, questions about working principles are giving way to complex questions of operating and business flexibility. Alfa Laval PureBallast remains at the forefront, with a capability range unmatched by any other system.
“The story of PureBallast is one of uncompromising innovation,” says Stephen Westerling Greer, Global Business Manager for the system. “Alfa Laval has faced the obstacles without resorting to shortcuts, and that policy is proving its worth as the market toughens.”
From protecting the environment to protecting business
During PureBallast’s early development, Alfa Laval’s target was to meet the IMO legislation without interference in vessel operations. When the first system achieved this by an excellent margin, the focus shifted entirely to vessels’ practical requirements. Already by the second generation, Alfa Laval was offering explosion-proof systems and making dramatic strides in energy efficiency.
Though the principles remain the same, PureBallast today boasts major advances in space usage, power management and breadth of capacity. Moreover, the PureBallast team has widened its focus from vessel requirements to business needs.
“Neither the operations on board nor the vessel’s area of operations should be affected,” says Westerling Greer of his team’s mindset. “The choice of ballast water treatment system should not be the major constraint on a vessel’s potential business or resale value.”
Performance in any waters
As Westerling Greer points out, PureBallast offers its owners exceptional freedom of movement. The system handles water in liquid form at frigid temperatures, and since January 2015 it has been certified for all water types: fresh, brackish and marine. “Three-water certification is important, and not only for those trafficking the Baltic or the Great Lakes,” Westerling Greer says. “Many ports we think of as brackish are farther from the marine end of the transition zone and closer to fresh water, which means the systems installed should be able to operate with freshwater constraints.”
Even in marine water, PureBallast performs where other systems merely get by. Large PureBallast systems of 1000 m3/h or more, which operate at just 52 kW in most port situations, can be ramped up to 100 kW when needed for harbours with low UV transmittance. The UV treatment in all PureBallast systems, which is already enhanced with AOT (advanced oxidation technology), can also be combined with fine filtration for performance in low-clarity and coastal waters. In this way, water with a UV transmittance of just 42% can be treated at full flow.
“The numbers are much more than a mathematical exercise,” Westerling Greer explains. “Some of the world’s key trading ports have water with poor transmittance, where the UV transmittance can be at or even below 50%. Other ports have temperatures that tend towards zero, or are essentially freshwater ports. Because water conditions are variable, a system operating at its limits near these parameters will run into difficulties, whereas PureBallast can treat water in all of these situations, providing it is liquid. The vessel’s operations are not compromised, which is an industry benchmark for other systems to be compared against.”
A part of setting the standard
All this puts PureBallast firmly at the technical forefront. Meanwhile, the company behind it has been selected as a consultant on several key panels that are developing standards and educating the market about the effectiveness of UV disinfection treatments.
“Our place on these committees is the direct result of Alfa Laval’s pioneering and long-term work with marine biology and UV-based ballast water treatment,” says Westerling Greer.
Developments on multiple fronts
Not surprisingly, Alfa Laval submitted a USCG type approval application for PureBallast in March 2015. Yet the approval process is just one of many developments currently underway.
As customers look towards the coming retrofit cycle, Alfa Laval is also expanding its PureBallast offering. Recent upgrades available in PureBallast 3.1 improve the system performance and simplify operation through a new human-machine interface. Retained with the upgrades are the flexibility in installation and a system design that allows the simplest, quickest maintenance of any ballast water treatment system on the market.
In addition, Alfa Laval is introducing a new PureBallast reactor for system sizes from 170 m3/h to 87 m3/h. This is a major expansion from the previous minimum flow of 250 m3/h, which will put PureBallast’s capabilities in the hands of a wide range of smaller vessels.
“As always, we’ve cut no corners in the development process,” says Westerling Greer of the new addition to the PureBallast family. “Smaller PureBallast systems will be a full match for their larger counterparts, with reactor construction in SMO, effective power management and compact, performance-enhancing CIP.”
Equal parts innovator and partner
Looking ahead, Westerling Greer is convinced of Alfa Laval’s continued role as an innovator. “For a decade, Alfa Laval has been pushing ballast water treatment forward,” he says. “We went through the learning curve early on to develop benchmark systems with a focus on the user’s operational and business needs. Having started as a pioneer, we are now a consultant with a strong role in educating the market.”
In addition, Westerling Greer emphasizes the growing diversity of challenges his company can meet. “Alfa Laval has not only the broadest service footprint, but also Performance Agreements, recommissioning services and other packages that offer peace of mind,” he says. “Still more business support services are currently being piloted with our customers. As the market moves forward and into the retrofit cycle, ship owners, ship operators and shipyards will find no partner more capable.”
To learn more about Alfa Laval PureBallast and Alfa Laval’s approach to ballast water treatment, visit www.alfalaval.com/pureballast3
For further information, please contact:
Stephen Westerling-Greer
Global Business Manager, PureBallast, Alfa Laval
Phone: +46 709 66 51 51
E-mail: stephen.westerlinggreer@alfalaval.com
Sofia Rugfelt
Marine Trade Press Manager
Marine & Diesel Division, Alfa Laval
Phone: +46 8 530 653 57
E-mail: sofia.rugfelt@alfalaval.com