IHM Maintenance
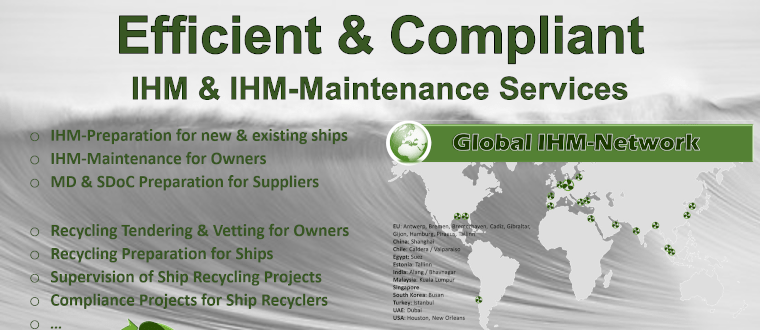
Implementation of Hong Kong Convention (HKC) of IMO and EU-Ship Recycling Regulation is my professional mission for more than 15 years. From cradle to grave, or shipyards, manufacturers, suppliers, ship owners to recyclers, or desk to dirt. I´m still loving to provide services and to develop customized solutions for efficient compliance.
Having a close dialogue with shipyards, shipowners and maritime suppliers on IHM and IHM-maintenance ever since, it seems to be the time to share some insights about how to evaluate compliant and cost-efficient “IHM-Maintenance”.
Crucial aspects for IHM-Maintenance
Until recently the 2020-deadline for Inventory of Hazardous Materials Part I – hazardous materials in structure and equipment (IHM) for existing ships visiting EU or flying an EU-flag was challenging. Not only caused by the number of ships, but also COVID-19 restrictions and the late action of quite a few shipowners. Now shipowners realise that it´s not enough to have a certified IHM onboard, but that it also has to be maintained. All this is subject to frequent controls by PSC and flag or class.
This is often seen as a bureaucratic burden and consequences of IHM-incompliance are heavy. A structured approach is seldomly applied and in parallel, maritime suppliers struggle with providing necessary documents like Material Declarations (MD) and Suppliers Declaration of Conformity (SDoC) as gathering the required information from their own supply chains proves to be difficult. Outsourcing of this unwanted task seems to be an option for owners and suppliers alike.
On the other side, some IHM-Experts see IHM-Maintenance as a good business opportunity. Quite a few of them are in a gold rush as seen at the Yukon River in the 19th century. Many gold diggers lacked experience, were unprepared and overlooked basic things, but all hoped for a bright future. That ruined many of them but their advantage was, that they had no clients operating extremely valuable assets who trusted them and depended on their performance.
No doubt, for owners, manufacturers and suppliers it is a new challenge to document presence and absence of hazardous materials within products and onboard ships. It´s also outside of their comfort zone and core businesses. However, many other industries have developed principles for material compliance data exchange decades ago which can be modified and applied for IHM-Maintenance. A sound understanding of such principles including full understanding and adoption to the ship specific requirements is the key for those taking care of IHM-Maintenance, which are not necessarily IHM-Experts.
Common practice for IHM-Maintenance
The core is identification of relevant order items and exchange with and support for suppliers. It is what it all starts with and a liability aspect. If this is not provided by the service supplier, or he´s not capable of doing it correctly, the cost of IHM Maintenance is increased and document quality reduced.
Some “service approaches” require from owners to collect suppliers’ documents and provide them to the service supplier once a month. In the same frequency ships are asked for onboard-changes relevant for maintaining the IHM. Consequently, most of the work, liabilities and time remains with the owner. The service fee and level is low, as like quality of IHM-Maintenance but owners remain heavily involved. If this is the approach by the service supplier, it seems better that the owners keep all in his own hands.
Many service suppliers are not selecting relevant order items and copy entire order lists for requesting documents from suppliers. One request for 27 items reviewed by us showed that only one of the items was relevant. What a waste of time and unnecessary workload for suppliers. No wonder that some start charging for the documentation. As open requests must be documented for ensuring reflection of accurate status of IHM, avoidable gaps for the ships are caused which will trigger problems during PSC-inspections and re-certification of IHM.
Another approach is that order or ship-specific documents are requested for items. This increases the documentation efforts for suppliers tremendously and indicates a substantial lack of understanding as the SDoC is company specific and MD a product or product group specific document.
The worst seen so far is, that a supplier forwards order data to a service supplier who copies all items into one MD and sends it to the requesting owners. As it´s done within few minutes it´s obviously without requesting information from sub-suppliers. It´s a matter of time when this approach, probably based on a simple software converter tool, will put one or both of them to court.
How to achieve efficient IHM-Maintenance?
Some indicators help detecting efficient approaches ensuring risk-free and compliant IHM-Maintenance. What counts is how smart, thought-through and transparent a service is for being cost-effective. We have joined hands with NautilusLog and developed an efficient software tool which combines our expert knowledge with artificial intelligence on secure servers in Europe.
Owners can be unburdened completely and only need to provide basic purchasing data (in our case automatically via an API). All other aspects including uninterrupted provision of updated IHMs and Maintenance Reports are provided by GSR Services. By using the software of NautilusLog the effort is reduced already, but still various bits and pieces count.
How can this be achieved best?
1. Reducing workload: Our evaluation of around more than 500k order items shows that less than 10% are relevant for IHM-Maintenance and require documents from suppliers. Knowledge on scope and exclusions for IHM-maintenance is key to efficiency and accounts for only 7% of the time required for IHM-Maintenance. Suppliers appreciate selective approaches instead of mass-mailings and we save them from unnecessary requests.
2. Compliance: Review of suppliers’ data and providing individual advice until documents are fully compliant is extremely important for safeguarding owners from risks related to inaccurate IHMs. This compliance-related task takes 86% of the time but is inevitable.
3. Shipboard action: Less than 1% of orders items require follow-up as they contain a documented hazardous material. We advise on labelling them and in case of installations or removals, details are provided by the crew via our online-tool within seconds. In case a banned substance is declared to be present we take immediate action and inform the supplier, purchaser as well as the ship.
4. Documentation Update: Any delivery of HazMat-containing items and changes onboard triggers automatic updating of IHM and IHM-Maintenance Report in our software tool in real-time. This keeps the IHM up to date and our tool provides full overview 24/7/365.
Optimization of supplier-ship interface
Even though our requests are kept to the bare minimum and are precise, suppliers´ face challenges and we take care of those with our tool as well. Suppliers are provided with their own “landing page” where forms and guidance is provided including a full overview of requests. In this overview they can directly upload documents by Drag&Drop. In case of repeated and already documented order items, the forms can simply specify the duration in which the documents can be used by specific or all customers. Also, in this landing page the chat function with our experts is embedded for ensuring timely exchange and guidance. Why do we include this in our IHM-Maintenance Services? This cooperative approach and guidance provided increases return and quality of documents drastically. This avoids risks and gaps in IHM documentation which is our core task for our clients.
We have similar services for supply chains overtaking their data-gathering and management challenges. Only integrated and thought-through approaches are the key to efficient material compliance data exchange.